Selecting the Right Pharmaceutical Container
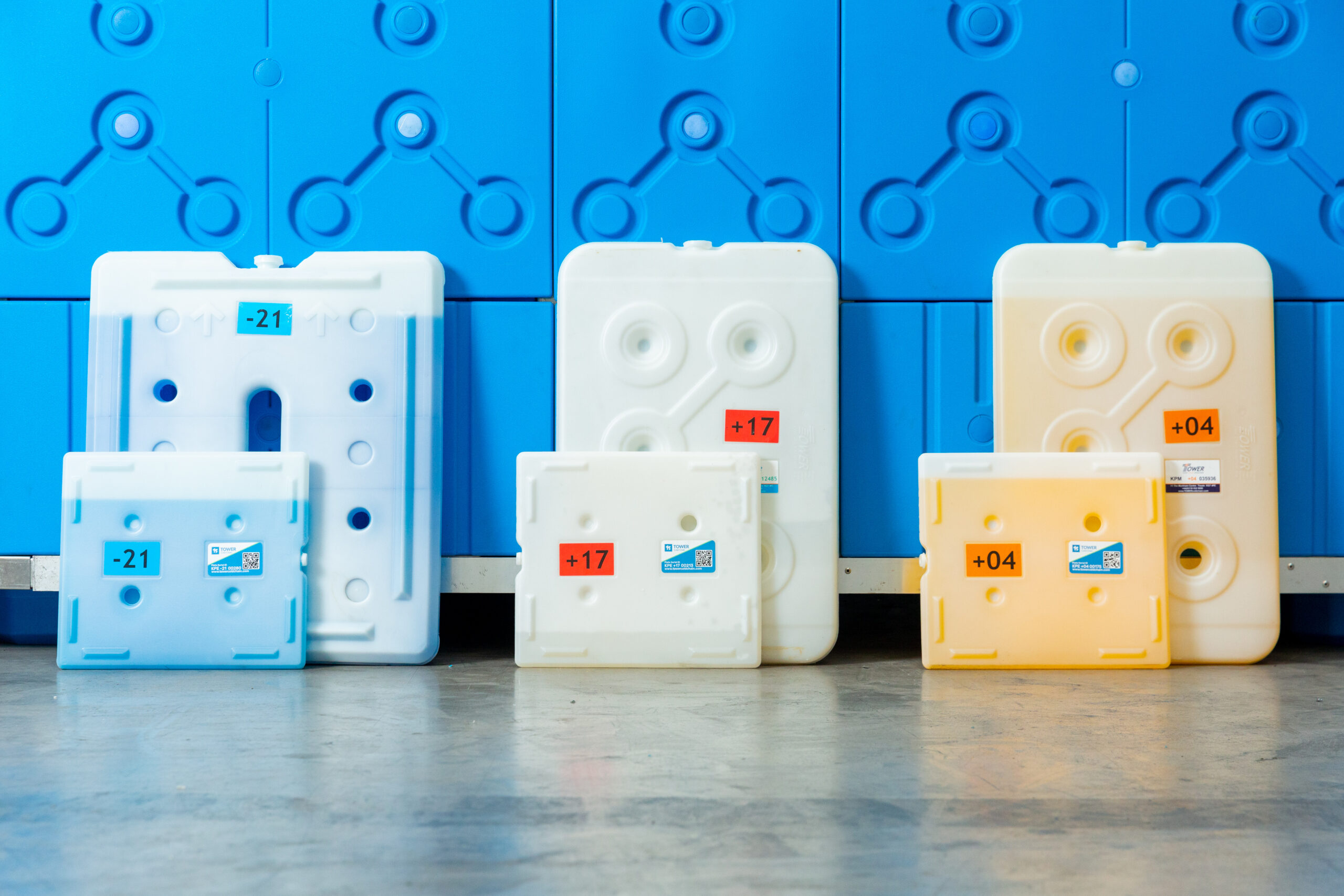
In the world of temperature-sensitive products, maintaining an unbroken cold chain is paramount. Whether it is vaccines, biologics, or other medications, the integrity of these products relies heavily on consistent temperature control throughout their journey. Thus, matching the appropriate pharmaceutical container to payload is a critical decision in ensuring that these goods arrive at their destination in optimal condition.
The core requirements
The baseline requirement for pharmaceutical logistics is that goods arrive on time, undamaged and with no temperature excursions. It’s here that the choice of pharmaceutical container can make all the difference.
A container needs to be robust enough to withstand the rigours of international freight and protect its cargo. Said container also needs to be optimised for temperature control to avoid excursions that render its cargo ineffective. And finally, the container should provide an optimal packaging-to-payload ratio.
And yet frequently, pharmaceutical containers aren’t optimised for the product they are shipping. For an example, shipping a half-empty box, even though smaller, more suitable sized containers are available on the market.
This lack of adaptability leads to shipping practices that are not sustainable. The efficient management of carbon emissions during the entire shipping process relies on making informed decisions – and its starts with matching the right container to product.
Understanding Payload Ratio
The payload ratio is a fundamental factor when determining the size of pharmaceutical containers. It refers to the ratio of product volume to the total volume of the container, encompassing both the product and any insulation or filler material. Striking the right payload ratio is crucial to avoid wastage of space while ensuring the product is adequately protected during transportation and storage.
Optimising the payload ratio means choosing a container size that allows for efficient use of space without compromising the product’s safety and integrity. Careful marketing analysis and testing is required to determine the ideal payload ratio for each product, considering factors such as fragility, stability, and required cushioning.
Take Tower’s KTEvolution container, developed specifically for the growing trend in shipments such as direct-to-patient, samples shipments, and clinical trials. As Tower’s smallest and lightest solution, the KTE is easily carried by 1-2 people, striking the optimum balance between high-performance and volumetric efficiency. Ideal for the transportation of pharmaceuticals, life-science, and biotech products that require an internal temperature from -60°C to +20°, the KTEvolution is a passive, reusable container offering thermal insulation without the need for external power or human intervention during transit.
Pallet Size and Container Compatibility
Pallets are a key component of pharmaceutical logistics, allowing for the organised and efficient movement of products through the supply chain. When selecting the size of pharmaceutical containers, compatibility with standard pallet sizes is essential.
Standard pallet sizes vary around the world, but adhering to widely accepted dimensions, such as the ISO pallet sizes, can help streamline logistics and reduce transportation costs. Choosing container sizes that align with these pallet dimensions helps maximise pallet utilisation, leading to better payload efficiency and cost savings.
Location and Storage Constraints
Geographical location and storage facilities significantly impact the choice of container size and use for pharmaceutical products. Storage capacities, warehouse layouts, and transportation limitations in specific regions may necessitate adjustments in pharmaceutical container choice to accommodate varying infrastructural constraints.
Adapting container sizes based on location-specific requirements ensures smoother operations and cost-efficiency in the supply chain. Flexibility in container sizing enables pharmaceutical companies to navigate different logistics challenges across various regions effectively.
For example, passive containers provide peace of mind in cases of disruption, whether this be diversions, breakdown or even labour strikes. Consisting of phase change materials intended to keep the internal contents of the package within a specific temperature range for a defined period of transport without any means of manual intervention or power source, this makes them ideal in parts of the world prone to power failures.
Making informed decisions
Making informed choices when matching the right sized pharmaceutical containers to products involves a careful consideration of payload ratio, pallet size, and location-based requirements. By optimising these factors, pharmaceutical companies can enhance operational efficiency, reduce costs, and contribute to a more sustainable future for the industry.