Quality Hub
The Quality Hub
As a trusted partner in the cold chain industry, we understand the critical role that regulatory standards and uncompromising quality play in delivering safe, effective, and reliable solutions.
With our deep expertise in Good Manufacturing Practices (GMP) and adherence to global regulations, we are committed to providing high-quality products and services that meet the stringent demands of the pharmaceutical world. Our goal is to ensure that every product and process aligns with both industry standards and your expectations, fostering trust and excellence in every collaboration.
Quality. Compliance. Innovation. That’s our commitment to you.
Regulatory Compliance
Our mission is to deliver superior service that not only meets but consistently exceeds customer expectations. By integrating our Quality Management System (QMS) as part of the Tower Integrated Management System (TIMS), aligned with ISO 9001:2015, we ensure the highest standards in compliance, quality, and service.
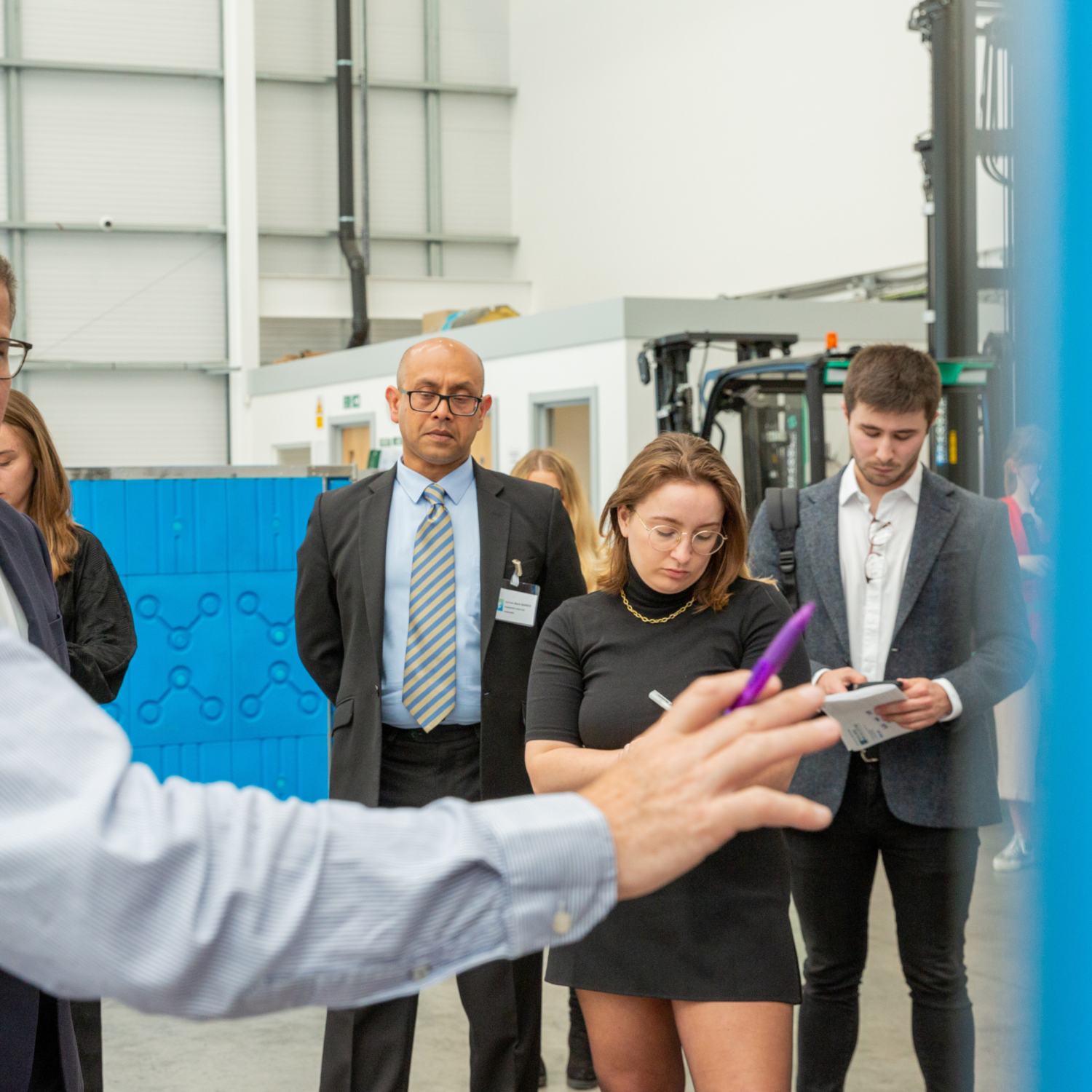
Supplier Auditing
We hold our suppliers to the same high standards as we hold ourselves. Through a structured audit program, both internally and with suppliers, we ensure that all components of our supply chain adhere to our strict quality and regulatory criteria. This program includes regular audits, evaluations, and performance assessments to ensure ongoing compliance with all applicable regulations and Tower policies.
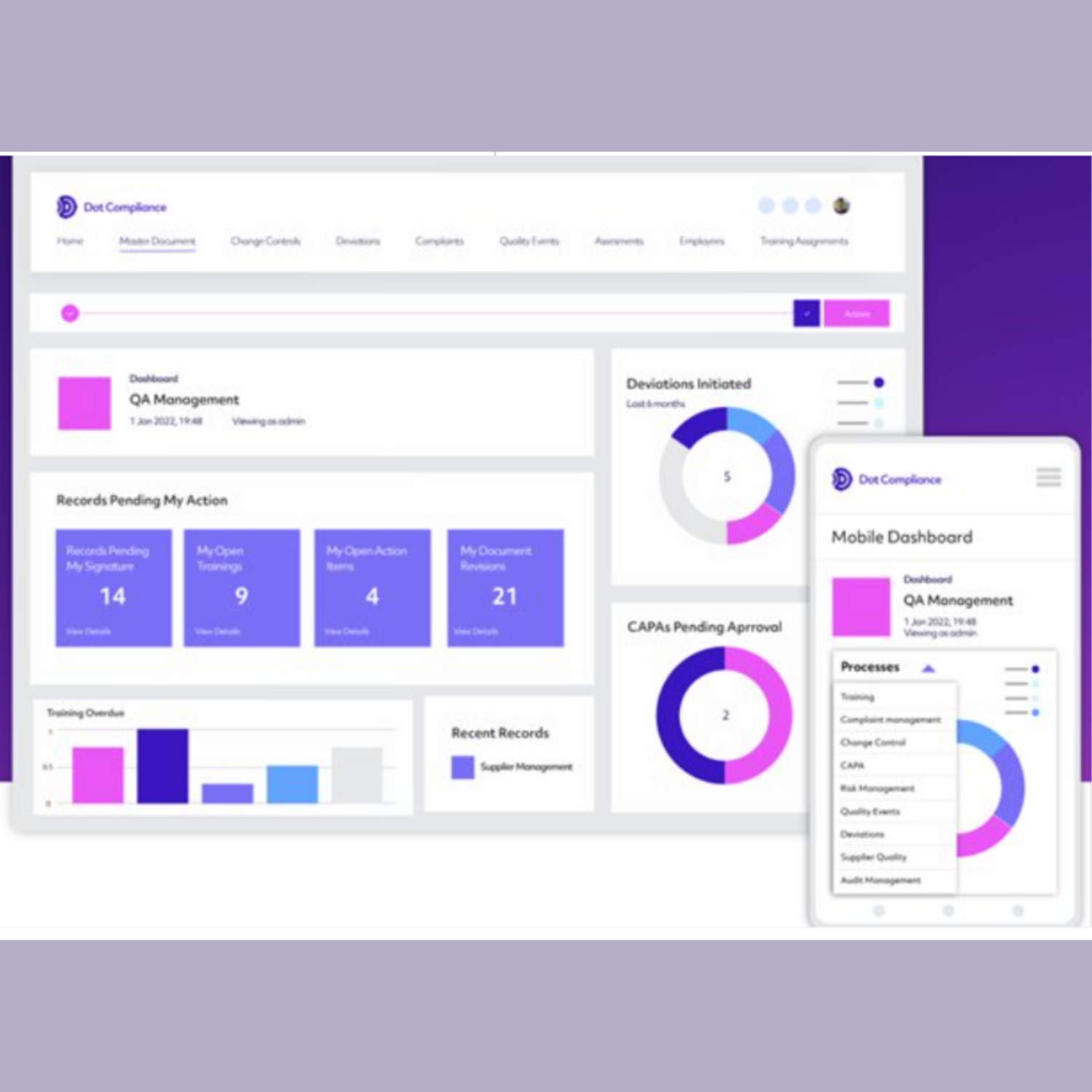
Risk Management and Monitoring
We have implemented rigorous risk assessment and monitoring processes through TIMS to proactively identify potential challenges, ensuring that quality, safety and compliance risks are identified, assessed, escalated, and mitigated at every stage. This vigilant approach allows us to consistently meet agreed-upon SLAs and regulatory requirements, ensuring safety and compliance across our operations.
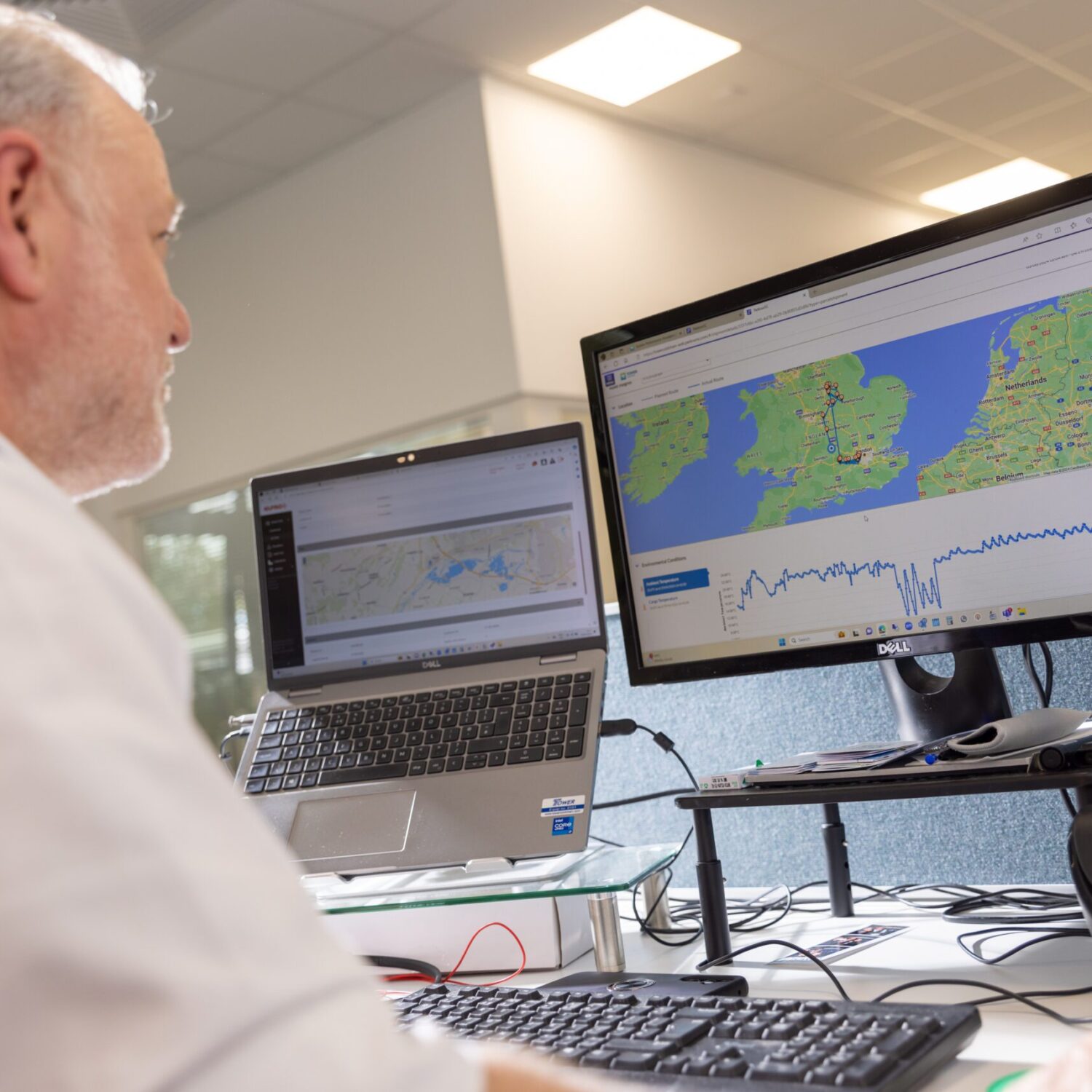
Traceability
Our commitment to traceability allows us to track cold chain continuity from origin to final delivery via the Tower Control Center, ensuring full transparency across the supply chain through the integration of data loggers in our containers. This level of detailed monitoring enhances our ability to meet regulatory requirements and address any potential non-conformances swiftly and efficiently.
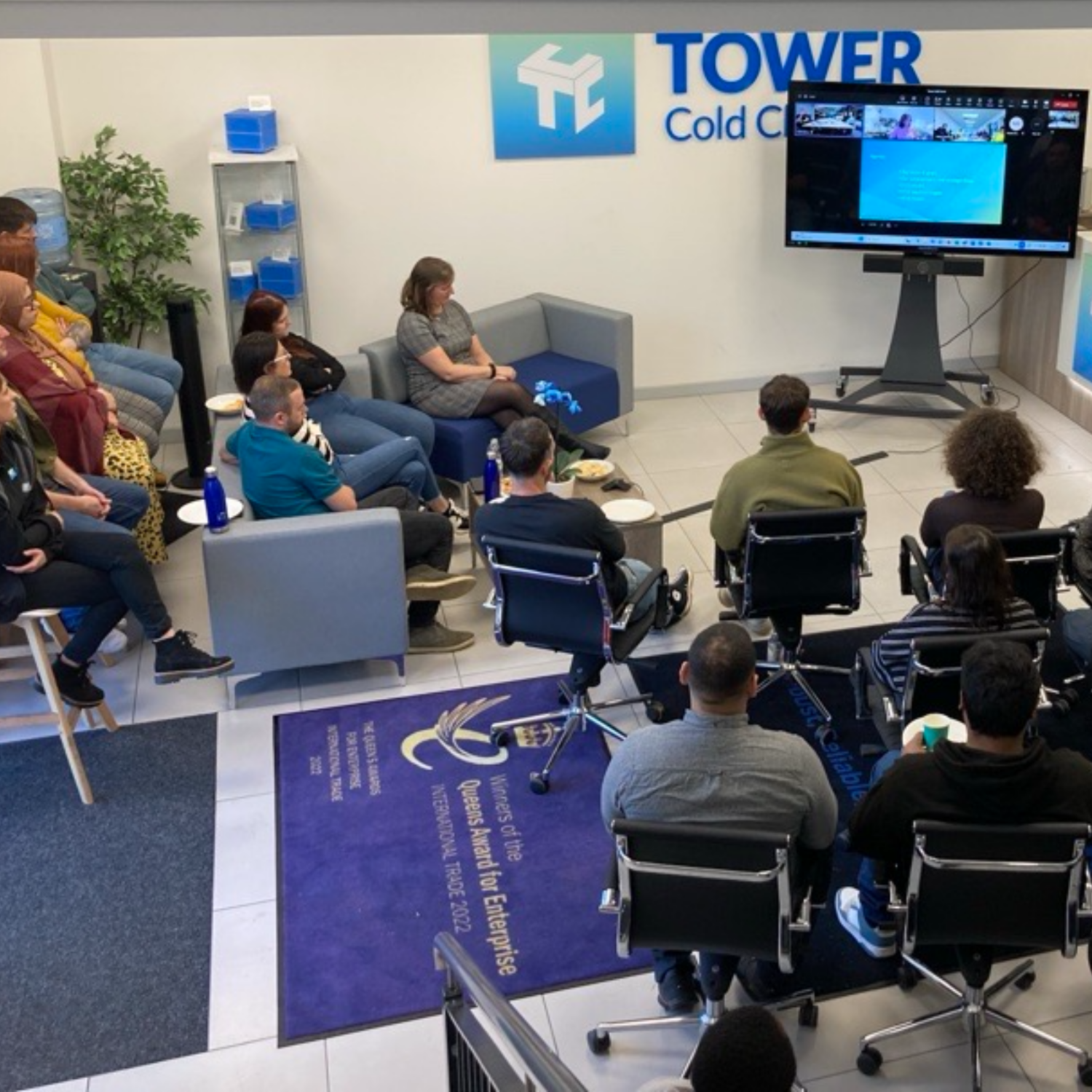
QMS and Training for Excellence
Our QMS is supported by comprehensive staff training programs, ensuring that every team member is equipped with the skills and knowledge required to maintain the highest standards of quality, safety, and compliance. Through ongoing development, we stay ahead of regulatory changes, ensuring our team operates at the forefront of industry best practices.
Tower Integrated Management System (TIMS)
Our approach is rooted in continuous improvement and a drive for excellence. TIMS supports our strategic objectives, enabling us to meet agreed SLAs, adhere to regulatory requirements, and maintain a safe and healthy workplace. TIMS Overview (Quality Manual) states that Management Review meetings are to be conducted annually, and as per the ISO 9001, ISO 14001, ISO 45001 relevant areas are covered within these meetings.
Quality Assurance
Our commitment to Quality Assurance and Quality Management is reflected in our adherence to global standards, such as ISO 9001 and Good Distribution Practice (GDP). We implement robust policies, practices, and disclosures that ensure the highest level of operational excellence across our entire supply chain to consistently provide products and services that meet customer and regulatory requirements.
96%
of employees trained
0.01%
temperature excursions
0
incidents of H&S non-compliance
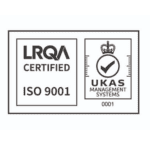
ISO 9001
This globally recognised standard for quality management systems (QMS) ensures we are consistently improving our operational efficiency, enhance customer satisfaction, and foster a culture of continuous improvement.
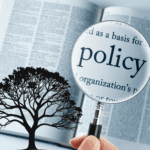
Quality Policy
Our Quality Policy reflects our commitment to delivering excellence in every aspect of our operations. By adhering to industry standards and continuously improving our processes, we ensure the highest level of product reliability, customer satisfaction, and regulatory compliance.
Quality Model
Our comprehensive quality model encompasses multiple key elements to ensure excellence. Quality Control focuses on verifying that products meet strict specifications through rigorous testing and inspection. Quality Assurance takes a proactive approach, preventing defects and guaranteeing consistency by implementing standardized processes. Quality Systems are integrated frameworks that drive continuous improvement, optimizing efficiency and performance. At the heart of this model is a strong Quality Culture, fostering integrity, accountability, and a commitment to excellence, ensuring that quality is a core value embraced at every level of the organization
Product Quality
We ensure every solution meets the highest performance and safety standards through rigorous product testing and precise calibration. Our dedicated processes guarantee reliability, durability, and compliance with global industry standards, providing you with trusted solutions for temperature-sensitive shipments.
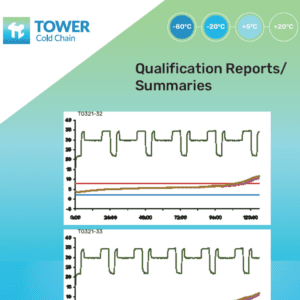
Qualification Summary Reports
To meet industry standards we qualify all our units against triplicate summer and winter temperature profiles based on ISTA 7D methodology. Qualification summaries and full summary reports are available on request for all product and temperatures.
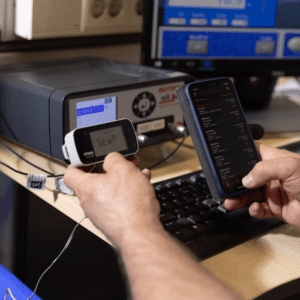
Calibration
We conduct in-house calibration of all loggers annually, guaranteeing precise data collection and reliable performance. Additionally, all temperature equipment undergoes yearly maintenance to maintain optimal functionality and accuracy. We also perform annual temperature mapping of conditioning reefers, ensuring consistent temperature control and compliance with industry regulations for safe storage and transportation. These practices are vital to maintaining operational excellence and ensure visibility and product integrity.
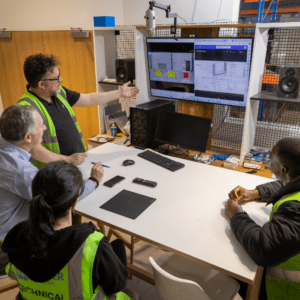
Innovation & Technology
Our product development team is dedicated to creating cutting-edge solutions that meet the evolving needs of industries requiring temperature controlled solutions. Every solution we design reflects our commitment to maintaining the integrity of temperature-sensitive shipments across the global supply chain.
Team & Culture
Governance & Organization
At Tower we consider that Quality is everyone’s responsibility. To achieve the highest standards in everything we do we empower our employees accross all functions and held our Senior Operation and Quality leaders accountable for periodically review the performance of the QMS to ensure that it continues to fulfill quality objectives, remains aligned with the strategic direction of the organisation, is supported by appropriate resources, and provides a pathway for escalation of quality, safety and compliance issues and risks. TIMS Overview (Quality Manual) states that Management Review meetings are to be conducted annually, and as per the ISO 9001, ISO 14001, ISO 45001 relevant areas are covered within these meetings. Tower currently conducts meetings quarterly.
“Quality isn’t just a department—it’s the foundation of our entire business and imbedded in our culture. By ensuring excellence in every process, we build trust, drive success, and create lasting value for our customers.”
Quality Assurance Manager at Tower Cold Chain
FAQ
Yes – TSOP015 – Calibration of Temperature Measuring
Temperature data loggers are calibrated annually internally. Reefers are calibrated/mapped internally.
Scales are calibrated once a year and a test weight is used. Production is all outsourced to our manufacturing suppliers, equipment is calibrated annually and records of calibration are reviewed at audits by the supply chain auditor.
Tower holds ISO 9001 (QMS), ISO 45001 (Occupational Health and Safety) and ISO 14001 (Environmental Management) certifications. Certified by Llyods Register (LR QA), a UKAS accredited body. Tower also holds EcoVadis Silver Award.
We carry an audit on a 24 month rolling cycle covering all departments, managed within Dot Compliance eQMS. H&S and Environmental Legal Compliance Audits, Quality and UK Operations Audits are conducted annually as per ISO Standard.
Yes – Customer Complaints/Non-conformances are raised in the eQMS as per our TSOP007 Non-Conformance Procedure, and managed electronically; investigation and full report is completed within 30 days.
Yes – Tower subcontracts the manufacturing process of its containers and plates, hubs and logistic services which is closely supervised, reviewed against SLAs and audited on a regular schedule. For Services that are subcontracted: quality checks are performed and reviewed by Tower. Plate fill, testing, calibration and qualification is done internally.
Yes – Tower has SOPs and INSTs, as well as a Quality Manual (TIMS001)
Yes – Quality Policy STA-0000232 is available on the Tower website.
Yes – we have a Change Control TSOP010 and our Change process is managed within the eQMS system: Dot Compliance: All changes that impact processes, systems or any documentation with risk to product or service is managed in DotCompliance under the Change Control Module as per TSOP010 Change control procedure.
Impact analysis is conducted and action items are raised within the eQMS, including notifying relevant parties of the changes that may impact them.
Yes – according to ISO9001:2015 Standard: we have TSOP002 Document and Record Control Procedure in place, which includes a table with various retention periods as per best industry practice and applicable statutory law.