Case Study: Optimising Biotechnology Logistics through Cold Chain Consultancy
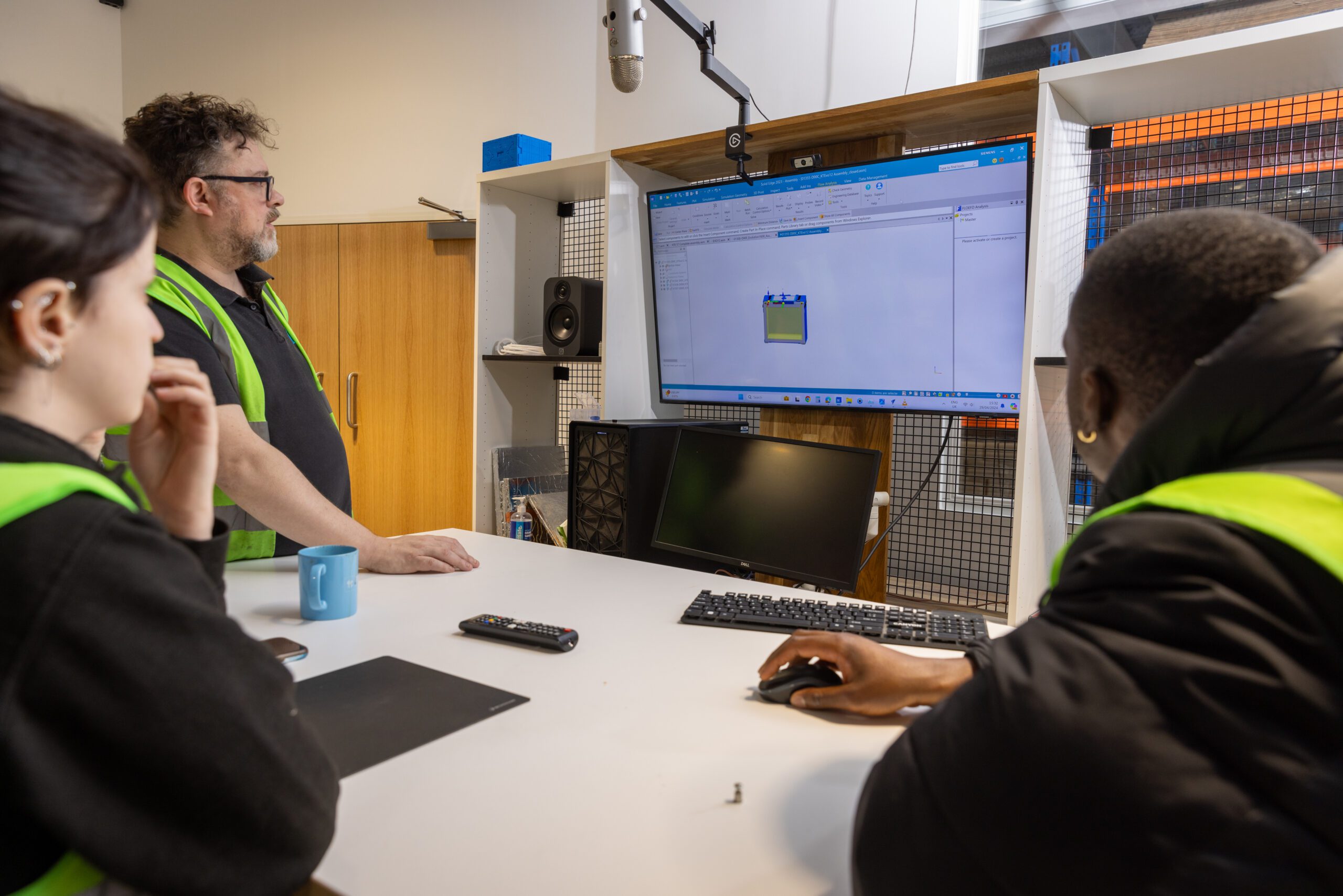
Introduction
Tower Cold Chain has established itself as a leader in temperature-controlled logistics, particularly in the pharmaceutical and life sciences industries. This case study details how Tower’s Product Development and Technical team collaborated with a global biotechnology leading organisation to create a bespoke cold chain solution that streamlined logistics, reduced costs, and ensured the integrity of high-value products.
Background
Since 2010, Tower Cold Chain has supported a global biotechnology business known for its innovative therapies. Over nearly 15 years of partnership, there have been no temperature deviations during transport, showcasing the reliability of Tower’s KT400 ultra-cold solution. The customer aimed to extend this dependable logistics framework to transport other bulk drugs and ingredients between manufacturing sites, prompting Tower Cold Chain’s Product Development and Technical team to develop a flexible packout solution to accommodate varying product formats and batch sizes.
Challenges
- High-Value Products: The biotechnology sector often involves transporting high-value goods that require stringent temperature control to maintain sterility and efficacy, to reduce the high financial impact of shipping failures.
- Material Sensitivity: At very low temperatures, the materials used in single-use primary packaging typically used are prone to fail, increasing the risk of product loss of sterility or containment resulting in a higher level of spoilage or wastage.
- Varied Packaging Needs: Each product format—such as bags or bottles— varies in quantity and batch sizes requiring different internal configurations to reduce the risk of breakage.
- Qualification Process: Traditionally, each shipment type required separate qualifications, leading to delays and increased costs. Our customer challenged us to help them avoid unnecessary re-qualification, while ensuring that products could be reliably protected.
The Solution
Tower’s Product Development and Qualification teams, based in Tower European Center of Excellence in Theale, worked with the customer to create a customisable packout platform that streamlined the qualification process while ensuring product protection.
Key elements of the solution included:
- Single Qualification Project: By establishing a base format for qualification, Tower significantly reduced the time and costs associated with multiple qualifications while ensuring compliance with quality standards.
- Customisable Internal Packing System: An internal packaging system was designed to adapt to various product formats and batch sizes, maintaining optimal support and protection.
- Ease of Use: The new system minimised complexity, enabling quick configuration and reducing risks associated with product movement during transit.
Implementation
The implementation process included:
- Bespoke Configuration Development: The technical team led by James Vann developed tailored internal parts for each product type, ensuring that all configurations adhered to the overall container qualifications.
- Training and Support: Tower provided comprehensive training, written and video instructions, and on-site visits to ensure seamless adoption by the customer and their third-party logistic and manufacturing partners.
Benefits
The project yielded significant benefits for the biotechnology customer:
- Consistent Shipping Solution: All products are now shipped using the KT400 under a single qualification framework.
- Diverse Packing Formats: Six different pack formats have successfully been shipped using the bespoke configurations developed by Tower.
- Time Savings: With an average qualification time of 10 months, this new packout development saved the customer an estimated 50 months (not including future additions) in qualification time, allowing quicker launches for future products.
- Standardisation: The simplicity of the new packing system has facilitated the standardisation of processes across global manufacturing and logistics partners.
Conclusion
This collaboration between Tower Cold Chain and the biotechnology firm illustrates the power of targeted cold chain consultancy in enhancing logistics for high-value products.
By addressing the unique challenges of temperature-sensitive goods, Tower has not only ensured product safety and integrity, but also enabled its customer to focus on innovation without the delays traditionally associated with cold chain qualifications.
James Vann summarised the project’s impact:
“Our solution allows our customer to leverage one system for multiple variations, providing ease of use for subcontractors and partners while reducing risk and cost, ultimately benefiting the customer commercially.”
This case study exemplifies how a strong partnership between supplier and customer can result in the development of innovative solutions in cold chain logistics to drive efficiency and effectiveness in the cold chain logistics.