Ensuring Pharmaceutical Product Integrity in Global Supply Chains
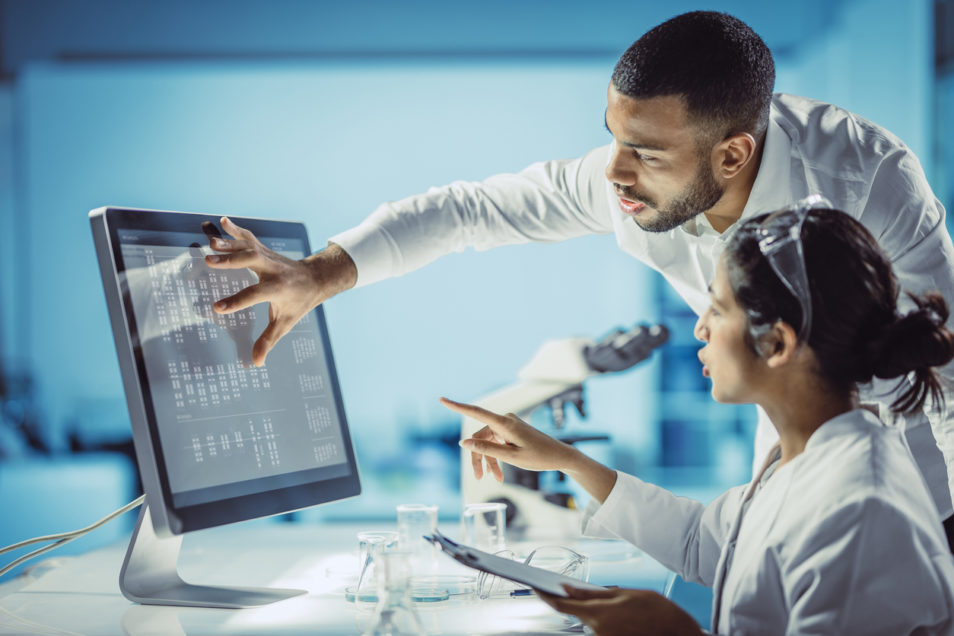
Issue Month: | November 2022 |
Within the pharmaceutical industry, product integrity is essential. From the very start of manufacture all the way to the arrival at the patient, it is vital that medical supplies are protected and maintained thoroughly across the supply chain.
At Tower, we understand that patient centricity is key. That’s why we take extensive measures to ensure pharmaceuticals are not at risk of temperature excursions when transported in our passive temperature-controlled containers.
Good Distribution Practice (GDP) requires medicines to be obtained from a licensed supply chain and to be carefully and consistently stored, transported, and handled in the correct conditions.
In any supply chain, without ensuring GDP and integrity, the potential risks to products are huge. For the pharmaceutical industry, such compromises are not only undesired but can affect the efficacy of the product. Worse, they might result in an adverse reaction to the patient’s health.
What can cause a temperature excursion? System failures, human carelessness, contamination, delay, or damage during transit are all possible reasons. However, there is a range of ways you can ensure product integrity and add that extra layer of security. This will benefit your pharmaceutical supplies, your business and your patients.
Technology and Innovation
Technology can play a very important part in quality control. At Tower Cold Chain, we use internal data loggers to ensure integrity by monitoring the internal temperature of our containers (ranging from -95°C up to 50°C). Using Bluetooth Low Energy Technology, each logger communicates wirelessly, sending accurate data to the cloud. Data is automatically downloaded throughout transit when in range of an InTemp Gateway device.
And, in the extremely rare case of a temperature excursion, the logger technology will notify our customers via text or email. This way, technology ensures door-to-door compliant payloads without any human intervention required during transit, optimising consistency.
Product Testing and Customer-Centric Manufacturing
Product testing is a fundamental step in ensuring a product’s reliability. This can be achieved by tangible, extensive quality assurance programmes, with such research influencing development and design.
Designed for reliability, Tower’s containers are carefully manufactured to be used in all climates, locations and at any time of year. With passive systems eradicating the need for manual intervention or energy source, it is no surprise that these containers are quickly becoming the sensible choice to de-risk shipping within these unpredictable times.
With our passive containers offering both internal temperature consistency and external, security we assure our customers 120-hour industry standard protection – 5 days’ worth of contingency.
Sterilisation
The re-usable nature of our containers means it is vital to provide a hygienic and sterile environment for pharmaceutical products. By using washable containers, microbial risks are massively minimised and product integrity is maximised.
Not only do reusable containers offer sterilisation and integrity protection, they also provide huge sustainability benefits compared to single-use, disposable containers that aren’t washable.
Tower’s units are completely reusable and washable, minimising any microbial contamination risks that also work to threaten integrity.
The importance of product quality control should always be priority in any pharmaceutical cold chain to protect business, products and, most importantly, the patients that receive them. By ensuring a sterile environment, innovation, proper GDP and thorough product testing, all participants in the pharmaceutical industry can work towards the same goal of maximum integrity.
Find out more on how Tower work to ensure product integrity: https://www.towercoldchain.com/pharmaceuticals-supply-chain/