Achieving cold chain sustainability: Realistic Net-Zero Goals
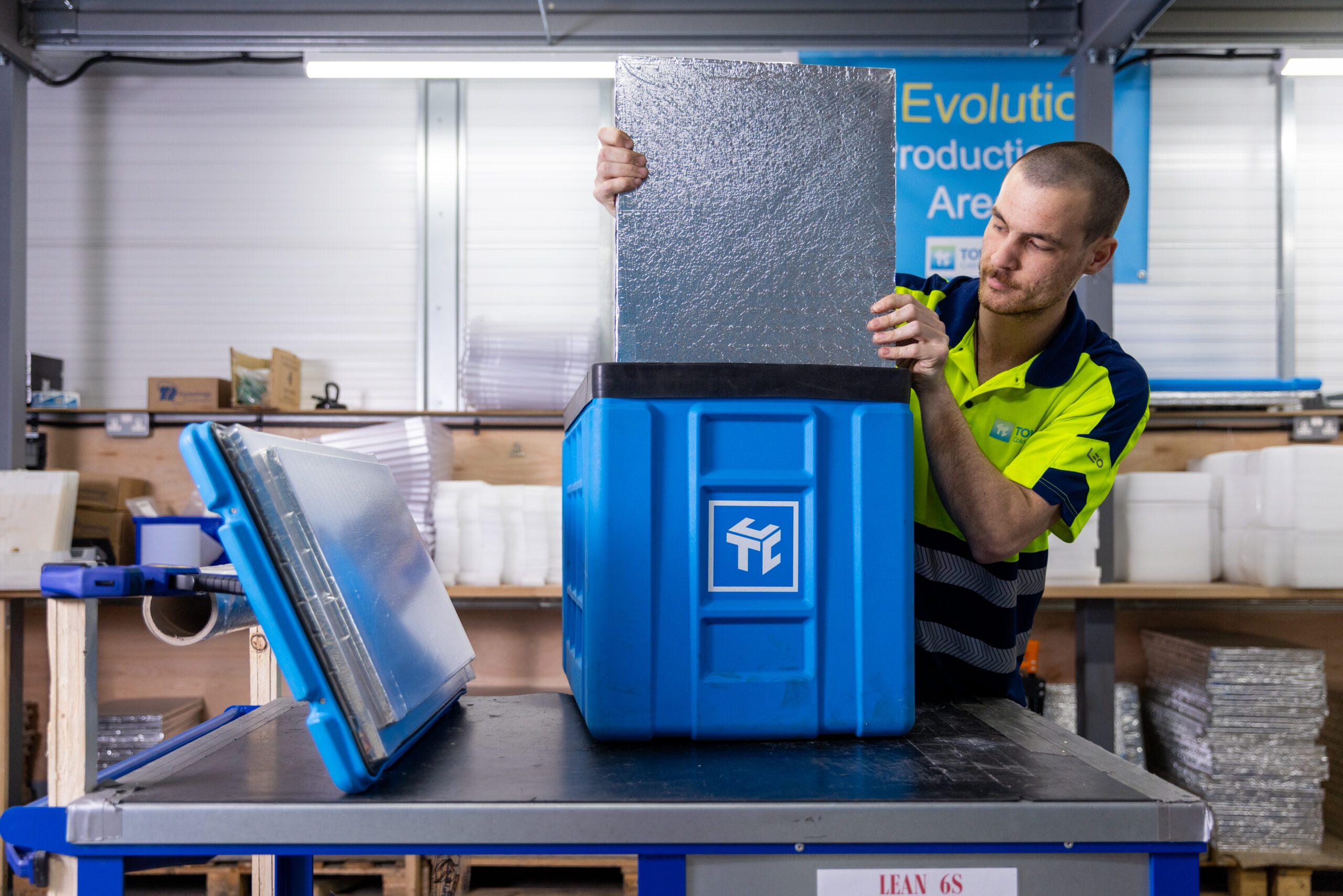
According to The Conversation, the pharma industry generates about 48.55 tons of CO2 equivalent per $1 million, 55% higher than the automotive industry’s emission intensity. Consequently, recent regulatory actions, such as carbon taxes and stricter policies, are not surprising. The demand for meeting ESG standards has led many pharma companies to reassess their processes and commit to becoming carbon neutral by 2030. Yet, achieving measurable sustainability requires practical steps, ensuring life-saving products reach patients safely and securely. This involves optimising the balance between operational efficiency, product protection, and sustainability across numerous complex steps and partnerships.
For the likes of temperature-controlled container providers, like Tower, these are playing a key role in helping pharmaceutical manufacturers achieve cold chain sustainability whilst on their journey to carbon neutrality.
Ensuring a reliable AND sustainable cold chain
The primary requirement for pharmaceutical logistics is ensuring goods arrive on time, undamaged, and with no temperature excursions. Despite the push for greener practices, three critical functions remain essential for shipping pharmaceuticals:
- Containers must withstand the rigors of international freight and protect their contents.
- Containers must be optimised for temperature control to prevent excursions that could compromise the cargo.
- Containers should have an optimal packaging-to-payload ratio.
Balancing requirements
The key challenge in pharma logistics is balancing incentives for sustainable solutions with the high costs involved. For temperature-controlled containers, it’s essential to consider the total cost of ownership. Beyond purchase and freight costs, hidden expenses such as the qualification and compliance process significantly impact the overall cost.
Manufacturers must ensure containers meet regulatory and performance standards, which involves extensive testing and documentation. This process is time-consuming and costly, with any errors leading to penalties. To save time and money, pharma companies often validate only a limited selection of containers. However, this can result in suboptimal shipping solutions, such as using half-empty boxes because more suitable containers haven’t been validated.
Customers might be aware their shipping solution is inefficient, leading to unsustainable practices. Achieving cold chain sustainability requires making informed decisions throughout the shipping process. However, the current validation and qualification system often restricts the ability to choose the most sustainable options.
Questioning the conventional
Forward-thinking suppliers of temperature-controlled containers are challenging the traditional method of qualification, helping manufacturers choose the right solution to reduce long-term carbon costs and ensure cold chain sustainability.
Advanced automation technologies, such as a digital payload calculator and a standardised cloud-based management system, simplify the three main stages of the equipment qualification process – design qualification, operational qualification, and performance qualification – saving time and money.
Such technologies centred around accurate data put the building blocks in place to help prove systems are installed correctly from day one, that they operate as expected, and that all processes perform to specification—meaning companies can onboard equipment much quicker, and at less cost.
Why Tower?
Achieving net-zero targets in the pharmaceutical industry requires an integrated approach, with cold chain sustainability playing a key role.
Tower Cold Chain challenges traditional qualification processes, enabling pharma manufacturers to match solutions precisely to payloads. Our fully reusable containers significantly reduce carbon footprints by staying in circulation longer, minimising environmental impact and packaging waste compared to single-use or semi-reusable alternatives. Robust design ensures these containers endure years of transportation, promoting reliable logistics and environmental responsibility.
And, with contingency built in, Tower’s passive containers maintain stable temperature-controlled environments without requiring any manual intervention or a power source during transit. With the International Air Transportation Association (IATA) reporting that over 50% of temperature excursions occur while shipments are under airline or airport control, passive systems using phase change materials (PCMs) are quickly becoming a sensible choice for pharmaceutical manufacturers to de-risk excursions and failures within unpredictable supply chains.
Interested in hearing more on how Tower achieves cold chain sustainability? Click here: https://www.towercoldchain.com/cold-chain-technology/